The Industrial Internet of Thing (IIoT) is revolutionizing industries. It is being used to monitor machinery, optimize energy usage, and streamline supply chains, making operations more efficient, safer and improving processes. IIoT is rapidly gaining acceptance in the oil and gas industry connecting the physical world to the digital one.
Below, we discuss the primary ways IIoT is changing oil and gas and the technologies that are driving the disruption.
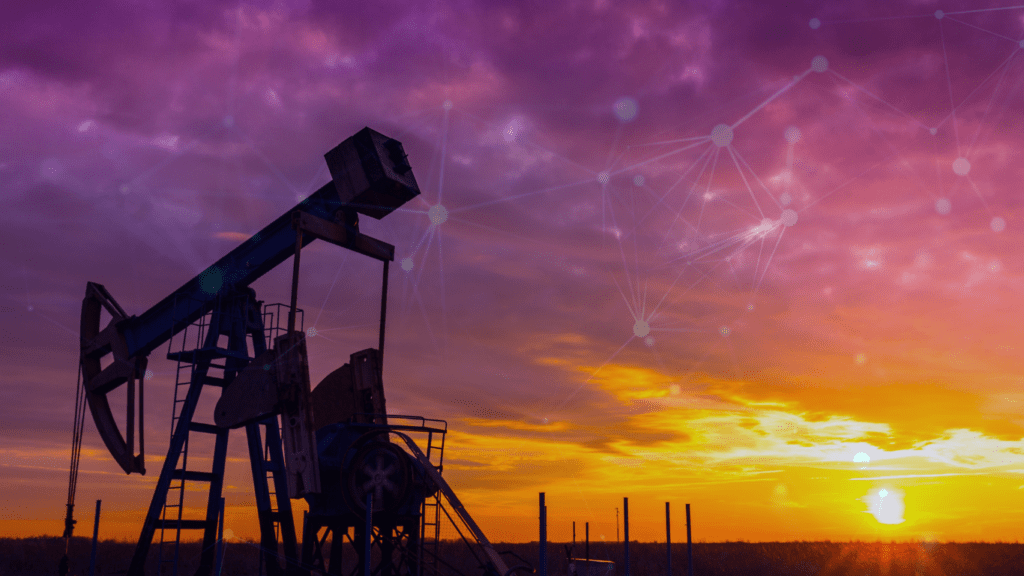
In this Article
Toggle1. Maintenance is Now Predictive, Not Reactive
The Change: Equipment maintenance is now predictive rather than reactive.
Traditionally, maintenance schedules were fixed or reactive: triggered only after equipment has failed and operations has been disrupted. This approach had lead to costly unnecessary and unplanned downtimes. Often this also came with higher repair costs and production outages.
IoT devices have revolutionized predictive maintenance by enabling real-time monitoring and advanced data analysis. Equipped with sensors, these devices continuously track critical parameters like temperature, vibration, and pressure, providing a constant stream of data on equipment performance. By leveraging AI and machine learning, IIoT systems analyze this data to detect patterns and anomalies, identifying potential issues before they lead to failures. This predictive capability allows for condition-based maintenance, where repairs are scheduled only when needed, reducing downtime and extending equipment life.
Example: Rockwell Automation’s Allen-Bradley industrial controllers and Opto22’s groov EPIC systems demonstrate how IIoT enables predictive maintenance. These devices integrate sensors to monitor key metrics such as motor vibration, temperature, and energy consumption in industrial equipment. For instance, Opto22’s groov EPIC system collects real-time data from connected machinery and uses built-in edge processing to analyze trends and detect anomalies locally. Similarly, Allen-Bradley controllers from Rockwell Automation work with software like FactoryTalk Analytics to process data and predict failures.
2. Wearables and Smart Devices in the Field
The Change: Worker safety is enhanced through wearables and smart devices.
Traditional real-time safety systems tied into SCADA primarily monitor equipment and process conditions to ensure operational safety. They would focus on preventing system-level failures like overpressure, leaks, or equipment malfunctions. While these systems are effective at safeguarding the infrastructure, they often lack direct integration with individual worker safety, relying instead on alarms and shutdown mechanisms that require workers to respond or evacuate.
IIoT-enabled safety solutions, however, can expand beyond the infrastructure and focus more on worker-centric safety by integrating wearable devices, environmental sensors, and mobile connectivity. These systems can provide real-time health monitoring such as tracking vital signs through a wearable device while also detecting immediate environmental hazards like toxic gas leaks, heat stress, or unsafe noise levels at the individual level. Unlike SCADA systems, which provide alerts to a centralized control room, IIoT devices can deliver immediate, personalized alerts to workers, supervisors, and safety teams via mobile devices or wearables, enabling faster, targeted responses. Furthermore, location-tracking capabilities, such as geo-fencing, help monitor worker movements in high-risk zones, enhancing situational awareness and improving rescue operations if needed.
Example: Honeywell’s Connected Worker Solution combines wearable devices like the BW Ultra gas detector with the cloud-based Safety Suite to monitor worker health, location, and environmental conditions in real time. These wearables send data to SCADA systems, enabling instant alerts and automated responses to hazards like gas leaks or heat exposure. The system ensures worker safety through proactive monitoring, geo-fencing, and integration with infrastructure controls.
3. Asset Integrity Management
The Change: Enterprise asset management solutions provide continuous monitoring of infrastructure integrity.
Traditionally, asset integrity management depended on periodic inspections and manual assessments of pipelines, rigs, and other critical infrastructure, often missing early signs of issues like corrosion or stress until they escalated into costly failures or downtime.
IIoT has revolutionized this approach by enabling continuous real-time monitoring with devices like those from Opto22, Rockwell Automation, and Beijer Electronics. These devices measure critical parameters like corrosion rates, pressure fluctuations, vibration levels, and structural stress. The data is analyzed using edge processing or sent to centralized systems, allowing operators to detect anomalies and predict potential failures well before they escalate.
Example: Opto22’s groov RIO system works seamlessly with sensors to monitor equipment like pumps and compressors in real time. By tracking vibration and temperature, it helps spot early signs of wear and tear, sending data to analytics platforms to predict issues before they cause breakdowns. Similarly, Rockwell Automation’s Allen-Bradley controllers, paired with FactoryTalk Analytics, are great for monitoring pipelines, keeping an eye on pressure and structural health. These systems give operators the insights they need to catch problems like leaks or corrosion early, saving time and money while keeping operations running smoothly
Oil & Gas Automation Case Studies
Alarm Rationalization in Oil & Gas
Automating Sand Removal Management in Oil & Gas
Automate your oil and gas operations.
4. Remote Operations are Reducing the Need for On-Site Visits
The Change: Remote monitoring and control of upstream sites.
Traditionally, upstream operations relied on frequent on-site visits for monitoring and manual adjustments, leading to high costs, increased safety risks, and slower response times. While traditional SCADA systems improve efficiency by centralizing data collection and providing some remote monitoring capabilities, they are limited in scope and require significant infrastructure investment.
IIoT is revolutionizing remote operations by leveraging advanced connectivity, cloud computing, and edge processing to provide real-time data and control from virtually anywhere. Unlike SCADA, which often focuses on process-level monitoring, IIoT enables comprehensive visibility across equipment, processes, and environmental conditions, even integrating predictive analytics to identify issues before they arise. This shift reduces dependency on on-site personnel, enhances operational agility, and improves safety by minimizing the need for human presence in hazardous or hard-to-reach locations, all while offering a more scalable and cost-effective solution.
Example: GE Digital’s remote monitoring solutions enable centralized management of multiple sites, improving operational efficiency and reducing travel-related costs. By leveraging IIoT, companies can ensure safer and more streamlined operations.
5. Energy Efficiency
The Change: Optimized energy consumption in upstream operations.
IIoT has transformed energy management by enabling real-time monitoring, data-driven decision-making, and proactive optimization of energy use. Unlike traditional reactive approaches, IIoT systems leverage connected sensors, advanced analytics, and automation to identify inefficiencies, predict potential issues, and recommend corrective actions. This shift allows industries to reduce energy waste, lower operational costs, and improve sustainability. By providing a continuous stream of actionable insights, IIoT empowers organizations to transition from passive energy management to a dynamic, intelligent framework that enhances efficiency and supports long-term environmental goals.
Example: Specific IIoT solutions, such as those from Rockwell Automation, Beijer Electronics, and Opto22, deliver targeted capabilities for energy management. Rockwell’s smart sensors and analytics tools enable real-time monitoring of energy consumption and predictive maintenance, helping to prevent inefficiencies before they escalate. Beijer’s HMI systems provide user-friendly interfaces for operators to visualize energy data and control equipment with precision, ensuring optimal performance. Opto22’s edge computing platforms process data locally at the source, enabling rapid decision-making and reducing reliance on centralized systems.
More on HMI:
What is High Performance HMI?
6. Integrated Data Platforms
The Change: Unified platforms for data integration and analysis.
Data in upstream operations was often siloed across different systems, making it challenging to achieve a unified view of operations. IIoT-enabled platforms address this issue by integrating data from diverse sources into a centralized system, enabling seamless communication, better decision-making, and improved coordination. These integrated platforms break down data barriers, providing operators with real-time insights and a holistic understanding of their operations. By connecting previously isolated systems, IIoT fosters cross-functional collaboration, enhances operational efficiency, and supports more informed strategic planning.
Example: Inductive Automation’s Ignition is a leading example of an integrated IIoT platform, designed to unify data from disparate systems into a single, centralized interface. Its robust scalability, real-time data visualization, and seamless connectivity enable operators to enhance decision-making, improve cross-functional collaboration, and optimize operational efficiency across industrial environments.
7. Real-Time Reservoir Monitoring
The Change: Real-time monitoring of reservoirs using IIoT-enabled sensors.
Real-time reservoir monitoring has been revolutionized by IIoT-enabled sensors, which provide continuous data streams on critical conditions such as pressure, temperature, and flow rates. Unlike traditional manual measurements, which often led to delays and suboptimal decisions, IIoT solutions enable operators to make quick, informed adjustments to production strategies, reducing downtime and maximizing efficiency.
Example: Inductive Automation’s Ignition platform exemplifies this transformation, offering seamless integration of IIoT sensors and real-time data visualization for reservoir monitoring. By providing operators with instant access to critical reservoir data, Ignition helps optimize extraction methods, improve recovery rates, and extend the life of reservoirs, all while minimizing operational disruptions.
Conclusion
IIoT is transforming the upstream oil and gas industry by replacing outdated processes with smarter, data-driven solutions. From real-time monitoring to automation and compliance, these advancements enable companies to operate more efficiently, safely, and sustainably. By partnering with technology leaders like Emerson, Honeywell, and Siemens, companies can stay ahead in this evolving sector.
Learn more about oil & gas automation.
Learn more about the industrial internet of things:
IIoT Platforms
IIoT Security