Need help with complex PLC systems?
Contents
ToggleWhat is a programmable logic controller (PLC)?
A Programmable Logic Controller (PLC) is an industrial digital computer designed for the control and automation of manufacturing processes or machinery. It is used extensively in industrial settings to automate various types of equipment and processes. Here are some key aspects of a PLC:
- Programmability: Unlike traditional relay-based control systems, PLCs can be programmed to perform a wide variety of control functions. They use programming languages such as Ladder Logic, Structured Text, Function Block Diagram, Instruction List, and Sequential Function Chart.
- Robustness: PLCs are built to withstand harsh industrial environments, including extreme temperatures, humidity, dust, and vibrations.
- Input/Output (I/O): PLCs have numerous input and output ports to connect with sensors, actuators, and other devices. Inputs can include buttons, switches, and sensors, while outputs can include relays, solenoids, lights, and motors.
- Real-time Operation: PLCs are designed to operate in real-time, meaning they can respond immediately to input changes and control outputs accordingly.
- Reliability: They are known for their high reliability and are capable of running continuously for extended periods without failure.
- Communication: Modern PLCs can communicate with other PLCs and computer systems through various communication protocols, enabling integration into larger industrial control systems.
- Modularity: Many PLCs are modular, allowing for easy expansion and customization to meet specific control requirements. Modules can include additional I/O, communication interfaces, and specialized function modules.
PLCs are fundamental components in automated systems, driving efficiency, precision, and safety in various industrial applications.
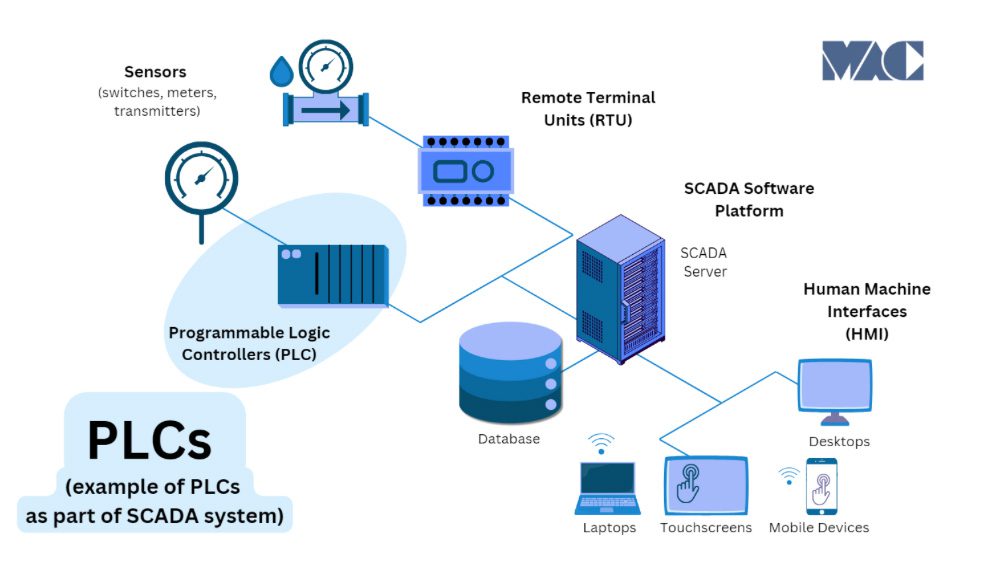
PLC programming services
PLC programming services encompass a range of activities involved in creating, testing, and maintaining the software that controls programmable logic controllers (PLCs). These services are crucial for automating and optimizing industrial processes.
At MAC Automation Inc., we offer comprehensive PLC programming services tailored to optimize and automate industrial processes. Our expertise includes system design, custom programming, integration with HMI/SCADA systems, thorough testing, and on-site commissioning. We also provide ongoing maintenance, troubleshooting, and operator training, ensuring reliable and efficient operation of your automation systems.
See below for a breakdown of the main components of PLC programming services:
System Design and Consultation:
- Needs Assessment: Analyzing the specific automation needs of a facility.
- System Architecture: Designing the control system architecture, including hardware and software specifications.
PLC Programming:
- Code Development: Writing the PLC programs using programming languages such as Ladder Logic, Structured Text, Function Block Diagram, Instruction List, and Sequential Function Chart.
- Custom Programming: Developing customized control strategies and programs tailored to the specific requirements of the machinery or process.
Integration:
- HMI/SCADA Integration: Integrating PLCs with Human-Machine Interfaces (HMI) and Supervisory Control and Data Acquisition (SCADA) systems for enhanced monitoring and control.
- Device Integration: Ensuring compatibility and communication between PLCs and other industrial devices such as sensors, actuators, drives, and robots.
Testing and Simulation:
- Simulation: Using software tools to simulate the PLC program in a virtual environment before deployment.
- Factory Acceptance Testing (FAT): Conducting tests to ensure the PLC program meets all specifications and functions correctly in a controlled environment.
Commissioning:
- On-site Installation: Installing the PLC system on-site and integrating it with existing systems.
- Start-up and Tuning: Initial start-up of the PLC-controlled system and fine-tuning the program for optimal performance.
Troubleshooting and Maintenance:
- Diagnostics: Identifying and resolving issues in the PLC program or hardware.
Upgrades and - Modifications: Updating and modifying PLC programs to accommodate process changes or improvements.
Training and Support:
- Operator Training: Providing training for operators and maintenance personnel on the use and troubleshooting of the PLC system.
- Technical Support: Offering ongoing technical support and remote assistance for any PLC-related issues.
Documentation:
- Code Documentation: Providing detailed documentation of the PLC programs, including flowcharts, function descriptions, and maintenance instructions.
- Compliance and Standards: Ensuring that the PLC programming and system design comply with industry standards and regulations.
PLC programming software
PLC programming software is a specialized software tool used to create, test, debug, and maintain programs for programmable logic controllers (PLCs). This software enables engineers and technicians to develop the logic and control sequences that PLCs use to automate industrial processes. Here are some key features and components of PLC programming software:
Programming Languages:
- Ladder Logic (LD): A graphical programming language resembling electrical relay logic diagrams.
- Structured Text (ST): A high-level textual language similar to Pascal or C.
- Function Block Diagram (FBD): A graphical language using blocks to represent functions.
- Instruction List (IL): A low-level textual language similar to assembly language.
- Sequential Function Chart (SFC): A graphical language for programming sequential operations.
Development Environment:
- Code Editor: A workspace for writing and editing PLC programs.
- Simulation Tools: Features that allow the user to simulate the PLC program in a virtual environment to test functionality before deployment.
- Debugging Tools: Tools to troubleshoot and debug the PLC program by monitoring variables and stepping through the code.
Communication:
- Device Connectivity: Interfaces for connecting the software to PLC hardware for downloading and uploading programs.
- Protocol Support: Support for various communication protocols (e.g., Ethernet/IP, Modbus, MQTT, Profibus) for integration with other devices and systems.
Library and Reuse:
- Function Libraries: Pre-built functions and blocks that can be reused in different programs, saving development time.
- User-Defined Functions: Ability to create custom functions and blocks for specific tasks.
Documentation and Reporting:
- Automatic Documentation: Features that generate documentation for the PLC program, including flowcharts, function descriptions, and maintenance instructions.
- Reporting Tools: Tools to create reports on program performance and diagnostics.
Version Control:
- Change Tracking: Keeping track of changes made to the program over time, facilitating version control and collaborative development.
Some popular PLC programming software packages include:
- Opto 22 PAC Control: For Opto 22 SNAP and groov PLC
- CODESYS: For PLCs with CODESYS runtimes.
- Altus BCS Tools: For Beijer Nexto Modular and Xpress PLCs.
- Rockwell Automation Studio 5000: For Allen-Bradley PLCs.
- Siemens TIA Portal: For Siemens PLCs.
- Schneider Electric EcoStruxure Control Expert (formerly Unity Pro): For Schneider Electric PLCs.
- Mitsubishi GX Works: For Mitsubishi PLCs.
- OMRON CX-Programmer: For OMRON PLCs.
These software tools are essential for developing efficient and reliable automation systems in various industrial applications.