Boost your industrial performance with an advanced DCS.
Contents
ToggleWhat is a Distributed Control System (DCS)?
A Distributed Control System (DCS) is a computer system used in factories to control and monitor machines and processes. It connects different parts of the factory, like sensors and machines, to a central computer. This central computer helps operators see what’s happening in the factory and make adjustments if needed. A DCS makes sure everything runs smoothly and safely, even in large and complex factories.
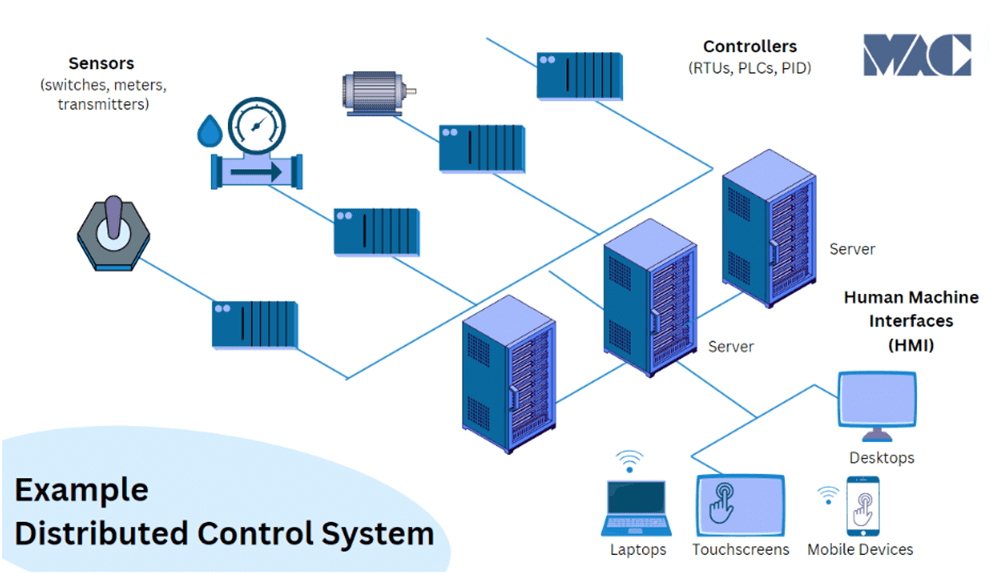
Evolution of Modern DCS systems
The evolution of modern Distributed Control Systems (DCS) has been marked by significant technological advancements and increased integration capabilities. In the 1970s, the first DCS systems revolutionized industrial control by replacing analog control panels with digital interfaces, allowing operators to manage processes from a central location. These early systems combined control and monitoring functions, streamlining operations and improving efficiency.
By the 1980s, DCS technology had advanced to include better integration of various components such as sensors and actuators. Sophisticated software enhancements allowed for improved data handling and process visualization, making the systems more user-friendly and effective. The 1990s saw the rise of networking technology, which enabled DCS systems to communicate more effectively with other systems like SCADA (Supervisory Control and Data Acquisition) and MES (Manufacturing Execution Systems). The adoption of open communication protocols improved interoperability and facilitated more cohesive industrial operations.
In the 2000s, advancements in computing power led to the incorporation of advanced automation features within DCS systems. Predictive maintenance, real-time analytics, and enhanced data processing capabilities became standard, with distributed computing improving system reliability and scalability. The 2010s marked the integration of DCS with the Industrial Internet of Things (IIoT) and Industry 4.0 technologies, leading to smarter, interconnected manufacturing processes. Real-time data analysis, cloud computing, and enhanced automation capabilities were at the forefront of this evolution.
In the 2020s, the focus has shifted towards improving cybersecurity measures to protect critical infrastructure. Artificial intelligence (AI) and machine learning (ML) have been integrated into DCS systems, making them more intelligent, adaptive, and capable of self-optimization. Modern DCS systems are now highly secure, interconnected, and intelligent, providing enhanced control and efficiency in complex industrial environments.
How does a Distributed Control Systems work?
Programming
SImilar to SCADA, Distributed Control Systems (DCS) are programmed using special software that tells the machines what to do. Engineers create instructions that help the system know how to react to different signals from sensors and control the machines to keep everything running smoothly.
- Architecture
The architecture of a DCS is like having a team of mini-computers spread out across a factory. Each mini-computer controls specific tasks but they all work together:- Controllers: These mini-computers are spread around the factory, each handling certain jobs.
Human-Machine Interfaces (HMIs): These are screens where operators can see what’s happening and make adjustments.
Communication Network: This is like the factory’s internet, connecting all parts of the system so they can share information.
Field Devices: These include sensors and machines that directly interact with the production process, sending data and carrying out commands.
- Controllers: These mini-computers are spread around the factory, each handling certain jobs.
- Manufacturing
In manufacturing, DCS helps automate and improve production. It constantly watches over machines and processes to make sure everything is working right. If something needs adjusting, the DCS can do it automatically. This helps make products faster and more reliably. - Distributed source control systems
While this term usually refers to tools like Git in software development, in DCS, it means that control tasks are spread across many mini-computers. If one mini-computer fails, others can take over, keeping the system running smoothly.
DCS is a network of smart controllers working together to manage and optimize factory operations, making sure everything runs efficiently and reliably.
Typical DCS applications
Distributed Control Systems (DCS) are used in various industries to control complex processes. Here are some common applications:
1. Chemical Plants:
DCS systems are essential in chemical plants where they control and monitor chemical reactions, mixing processes, and ensure that safety standards are met. They help maintain precise conditions for temperature, pressure, and flow to produce high-quality chemicals.
2. Oil and Gas Industry:
In the oil and gas industry, DCS is used to manage the extraction, refining, and distribution processes. It controls the flow of oil and gas through pipelines, monitors drilling operations, and ensures the safe processing of raw materials into usable products.
3. Power Plants:
DCS systems are crucial in power generation, whether in coal, nuclear, or renewable energy plants. They help control the production of electricity, manage turbine operations, and ensure the stability of the power grid.
4. Food and Beverage Industry:
In food and beverage manufacturing, DCS helps automate processes such as mixing, cooking, and packaging. It ensures that products are made consistently, meeting strict hygiene and quality standards.
5. Pharmaceutical Industry:
Pharmaceutical manufacturing relies on DCS to control the production of medicines. It helps maintain precise environmental conditions and manages complex chemical processes, ensuring that medications are safe and effective.
6. Water and Wastewater Treatment:
DCS is used in water treatment plants to control the purification process, manage the distribution of clean water, and monitor the treatment of wastewater. It helps ensure that water quality meets health and safety standards.
7. Paper and Pulp Industry:
In the paper and pulp industry, DCS controls the production process from raw material preparation to the final product. It helps manage the complex chemical and mechanical processes involved in making paper.
DCS applications span across various industries, including chemical plants, oil and gas, power generation, food and beverage, pharmaceuticals, water treatment, and paper production. They are essential for automating and optimizing complex industrial processes, ensuring safety, efficiency, and product quality.
Commonly asked questions about distributed control system
Difference with central control systems
A Distributed Control System (DCS) is a combination of both hardware and software. The hardware includes controllers, sensors, actuators, human-machine interfaces (HMIs), and communication networks. The software comprises the control algorithms, user interfaces, data processing, and monitoring tools that run on the hardware to manage and optimize industrial processes.
A PLC (Programmable Logic Controller) is used for controlling specific processes or machinery, while a DCS (Distributed Control System) is used for managing complex, large-scale processes across an entire plant.
- Programmable Logic Controller (PLC):
- Purpose: PLCs are small computers used to control simple tasks, like operating machines on an assembly line.
- Structure: They usually work alone and are very fast at handling specific jobs.
- Use: Great for straightforward, repetitive tasks in smaller setups.
- Distributed Control System (DCS):
- Purpose: DCS systems manage complex processes, like those in a chemical plant or power station, where many parts need to work together.
- Structure: They have multiple controllers spread out over a large area, all connected to a central system.
- Use: Ideal for big, complicated operations where everything needs to be closely coordinated
DCS (Distributed Control System) is used for controlling processes within a plant, while SCADA (Supervisory Control and Data Acquisition) is used for monitoring and controlling processes that are spread across multiple locations.
- Distributed Control System (DCS):
- Purpose: DCS is used to control and monitor processes within a single facility, like a factory.
- Structure: It has controllers spread out within the plant, with a central system that oversees everything.
- Functionality: Focuses on making sure the process runs smoothly and efficiently, with quick responses to changes.
- Supervisory Control and Data Acquisition (SCADA):
- Purpose: SCADA systems are used to monitor and control processes that are spread out over large areas, like water supply systems or electrical grids.
- Structure: Includes remote units and sensors far apart, all connected to a central monitoring system.
- Functionality: Gathers data from these remote locations and helps operators see the big picture and make decisions.