How San Francisco used advance IIoT technology to power public transportation and in the process, reduce noise pollution and the prospect of diesel spills.
A 70-foot (21-meter) catamaran called the MV Sea Change transports 75 passengers along the waterfront between Pier 41 and the downtown San Francisco.
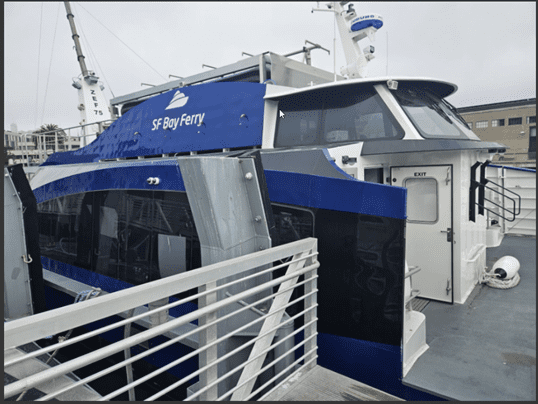
Problem:
Most U.S. ferries run on diesel, creating harmful noise and chemical pollutants.
Noise Pollution
Diesel engines are loud, causing noise pollution that affects marine life and human communities.
Health and Environmental Risks
Emissions contain harmful substances like particulate matter and nitrogen oxides, which can cause respiratory issues and other health problems for people living near ports and waterfronts.
Diesel spills can harm marine ecosystems and wildlife.
Objective:
Design a sustainable alternative to diesel-powered marine vehicles.
Facing stricter regulatory environmental regulations and the increasing costs associated with non-compliance, All American Marine, MAC Automation and Blu Fin Marine collaborated on a ground-breaking marine automation solution.
Tags
Tags Implemented
Screens
Pages
Alarms
Alarms total
Technologies deployed
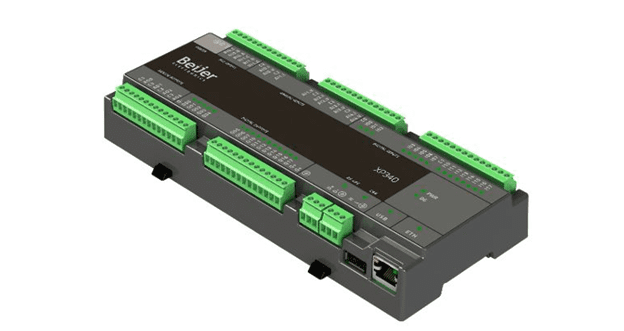
Nexto Xpress BCS-XP340 compact controller (PLC)
Using seven Beijer Electronics Nexto Xpress BCS-XP340 PLCs, hundreds of lines of ladder logic were designed to control motor fans, cooling fans, monitor dozens of analog and discrete inputs throughout the various parts of the vessel. This fully integrated and customized system provides real-time and historical alarms that allows a safe and reliable operation of the system. The PLCs were programmed with the CODESYS software provided by Beijer. All PLCs are networked together via a TCP/IP network and report back to a common HMI described below.
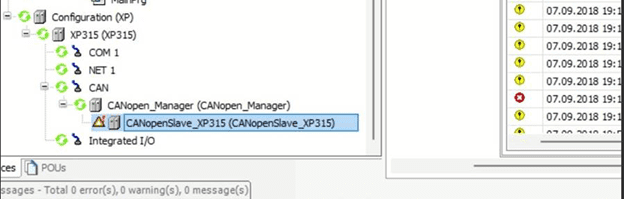
CANOpen_Manager (CANBUS)
To provide real-time data from the engine control system, CANBUS was deployed using the Nexto CANOpen_Manager. A controller area network (CAN) is a vehicle bus standard designed to enable efficient communication primarily between electronic control units (ECUs). This robust and flexible communications standard common in many engine applications was originally developed to reduce the complexity and cost of electrical wiring in automobiles through multiplexing. Today, this standard has permeated through power generation, industrial control systems and nearly all verticals MAC supports.
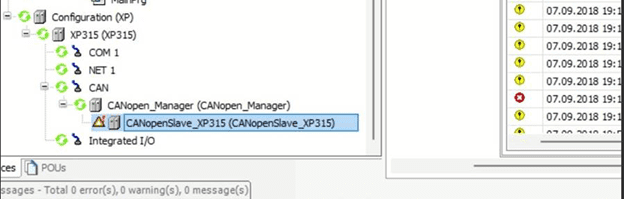
Beijer X2 Extreme Human Machine Interface (HMI)
The Beijer X2 HMI brings all the data from the PLC’s and ECU’s together via OPC and CANBUS over Ethernet TCP/IP to provide a single user interface to monitor and control all critical components of the vessel.
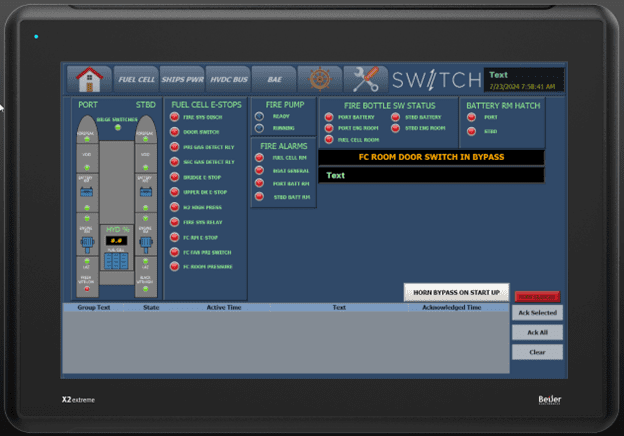
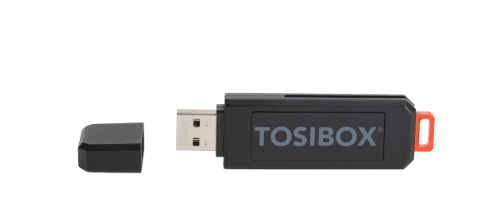
TOSIBOX® Key
TOSIBOX® Key is an intelligent cryptoprocessing device that enables a secure connection between you’re the vessel and remote computers to allow support of the system anytime anywhere. TOSIBOX® Nodes, allows for full visibility and control over the network devices connected to the Node. Connections are established through a secure, encrypted VPN tunnel over the Internet or other common WANs and LANs, and permissions can be easily granted, revoked and configured in an unlimited number of ways.
Outcome
Through the hard work of many teams that MAC has been grateful to work alongside of, the integration of automation, mechanical, electrical and structural engineering has allowed for the maiden voyage of the San Francisco Sea Change. This novel nautical next generation node of transportation will surely usher in a new era of clean, quiet and responsible transportation that will be sure to inspire more such vessels to follow in the future.
Read more about the MV Sea Change project on MSN.com.
Team
Meet the automation engineers that executed this project: